Various green technologies have emerged in recent years with the potential to cut CO2 emissions in heavily polluting industrial processes.
These advancements often allow the use of renewable energy sources like solar, wind, hydro, and geothermal power to replace fossil fuels and the adoption of energy vectors such as green hydrogen.
The development of green hydrogen, green steel, green cement, and carbon capture and storage are among the most exciting advances, but what are these technologies, and where are we currently in the race to decarbonise the heavy industries?
Green Hydrogen
Green hydrogen has various applications as a vehicle fuel or for industrial use.
It is easy to store, and its adoption has the potential to reduce emissions in hard-to-abate sectors – those sectors that are particularly difficult to decarbonise, such as the steel or cement industry.
Green hydrogen is often referred to as an energy carrier, meaning it can store and deliver energy from one place to another rather than being a primary energy source. It is produced using renewable energy sources through the process of water electrolysis. In this process, an electrolyser uses renewably generated electricity to split water molecules into hydrogen (H2) and oxygen (O2). The electrical current flows through the water, initiating a reaction that separates it into these two gases.
The extracted hydrogen is then purified and used in a variety of ways. It can be easily stored and supplied back to the grid when energy demand is high. It can also be used as a feedstock in the production of ammonia and other chemicals and in the cement and steel industries to reduce carbon emissions. Green hydrogen can also be used to power fuel cell vehicles, releasing only water as a byproduct.
Although less than 0.1% of global hydrogen production currently comes from electrolysis, there are hopes for rapid growth. The International Energy Agency forecasts that to meet its Net Zero Emissions Scenario, global green hydrogen production needs to reach 50 million tonnes by 2030, accompanied by a potential cost reduction of 30-50% during that time frame.
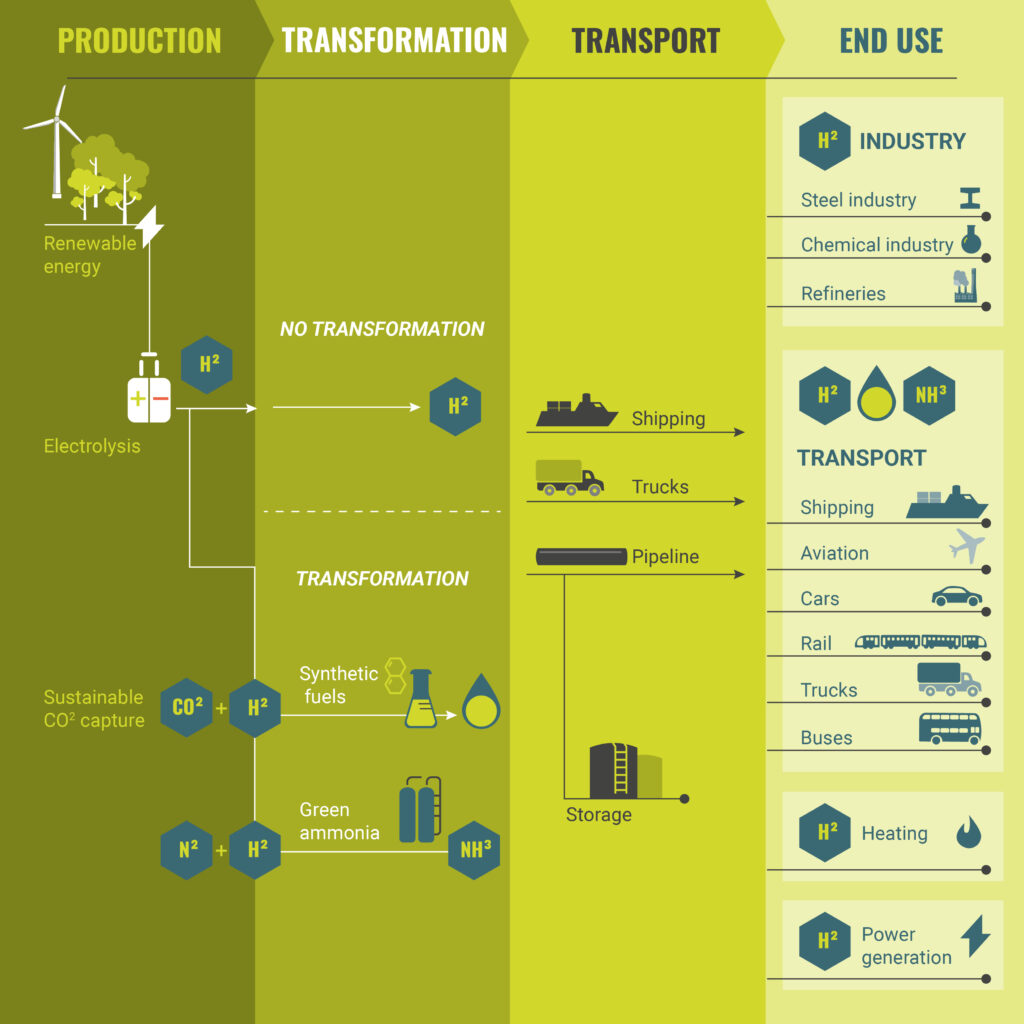
Green Steel
Steel is the most commonly used metal in the world. It is used to construct buildings and produce everyday goods like cars, bikes, and washing machines.
However, it is also the most energy-intensive and highest carbon-emitting industry: it accounts for between 7 and 11% of global CO2 emissions, depending on the source.
Urgent decarbonisation of this sector is vital to keep climate change at bay, and the transition to greener steel holds immense promise.
Green steel refers to methods that aim to reduce or eliminate CO2 emissions in the production process.
Steelmakers can achieve this in multiple ways, including:
- By using green hydrogen instead of coal in steel production as a reducing agent in the blast furnace
- By replacing coal-fired blast furnaces with electric arc furnaces fueled by renewable energy. Electric arc furnaces are more energy efficient and melt recycled scrap steel to produce new steel.
- Using carbon capture and storage technologies in the steel plants that use traditional furnaces.
But while the technological breakthroughs are exciting, various stumbling blocks still need to be solved in the large-scale adoption of green processes. Higher costs and the limited availability of green hydrogen are among the main ones and could cause costly delays in decarbonising this highly polluting industry.
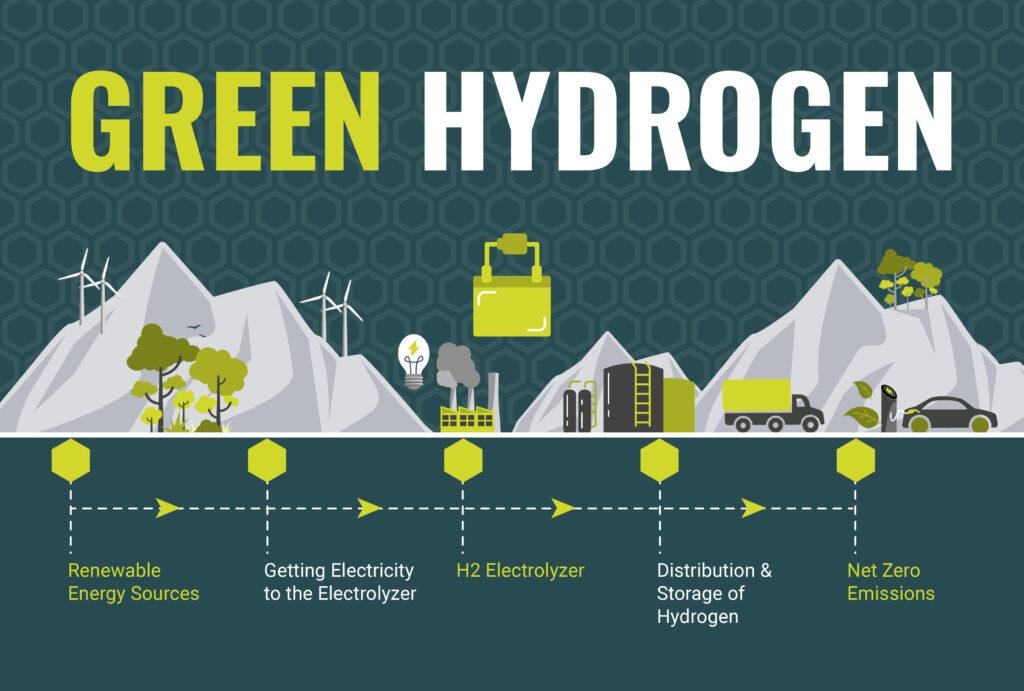
Green Cement
Aside from water, cement is the most globally consumed resource. With traditional cement production responsible for around 8% of global carbon dioxide emissions (0.58 tonnes of CO2 per tonne of cement produced in 2022) due to the energy-intensive process and the calcination of the limestone when heated, it is essential to find a more sustainable, environmentally friendly version of this product.
Green cement explores alternative production techniques aiming for carbon negativity. It is termed “green” when created through carbon-negative methods. Green cement seeks to minimise energy consumption during production by utilising substitute raw materials like fly ash and slag to replace limestone, making it a more eco-friendly option.
Whereas traditional cement production uses a large amount of natural gas in the heating process, green cements such as calcium sulfoaluminate cement (CSA) require far lower temperatures for the cement to be calcined (1,250℃ compared to the 1,500℃ usually needed). In addition, because the CSA clinker is softer than normal cement, it uses less energy in the grinding process.
Aside from CSA there are multiple other types of green concrete including:
Geopolymer cement – using raw materials like industrial and agricultural waste products.
Magnesium Oxychloride cement – using byproducts of magnesium mining.
Sequestrated Carbon Cement – this converts CO2 into a mineral and then traps it in the concrete.
Carbon Capture and Storage
Carbon Capture and Storage (CCS) is a crucial technology in combating climate change. It captures carbon dioxide emissions from industrial processes, power plants, and other sources before they can enter the atmosphere. Once captured, the CO2 is transported and securely stored deep underground, significantly reducing carbon emissions released into the environment.
Important monitoring is required during this process:
- Ensuring the storage is long-term and safe
- Understanding how the CO2 will behave underground
- Keeping record of any potential leakage
- Accurately measuring the amount of CO2 being stored.
Carbon capture and storage holds significant potential for mitigating the adverse impacts of greenhouse gas emissions and fostering a more sustainable energy landscape.
Cutting costs
However, the high costs related to these technologies have stalled their widespread adoption. Implementing carbon pricing or emissions trading can incentivise companies to explore and invest in cleaner technologies. A World Bank study highlights a notable surge in investments in nations adopting carbon pricing mechanisms, stimulating renewable energy and energy efficiency investments, and resulting in a 16% reduction in greenhouse gas emissions in sectors covered by these mechanisms (European Environment Agency). This emphasises the efficacy of carbon pricing in spurring research and investment in eco-friendly technologies.